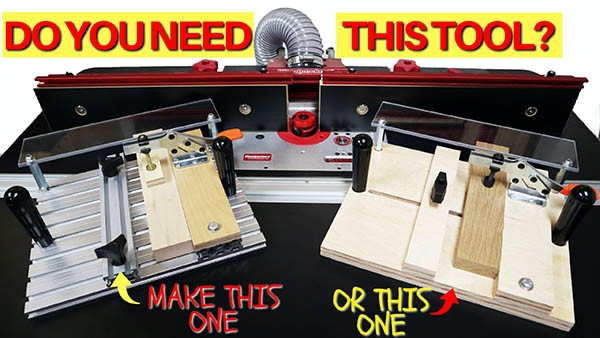
I’ve made lots of frame and panel doors just using my table saw. You can make a simple clean door using just one tool! However you are limited to making a simple door with no profiled inner edges. To really up your game and achieve a more decorative door you need to use rail and stile router bits to cut the grooves,profiled edges and most importantly the cope cut that allows the rails to “mate” perfectly with the stiles. One of the most useful jigs you can have for the router table is the coping sled. It can help make the cope cut much more efficient, accurate and safe.

DID YOU KNOW: You can follow me on these social media platforms!
Instagram · YouTube · Facebook · Pinterest
Materials & Supplies | |
Plywood Sled | Aluminum Sled |
Some parts I ordered from https://www.mcmaster.com/ | Aluminum Extrusions ordered from https://us.misumi-ec.com/ |
(Base) 3/4″ Scrap Plywood 10″x12″ | (Base) Misumi part#HFSQN4-15250-300 |
(Stationary Fence) 3/4″ Scrap Plywood 3″x 10″ | (Stationary Fence) Misumi part#HFS5-2060-250 |
(Sliding Fence) 3/4″ Scrap Plywood 2″x 10″ | (Sliding Fence) Misumi part ##HFS5-2040-250 |
(2) Tapered Handles (1/4-20 thread) McMaster Carr part #62385K32 | same |
(2) 2″ Hex Standoffs (1/4-20 thread) McMaster Carr part #93620A199 | same |
(2) 1/4 -20 Hex Bolts | same |
(1) 3″x 12″ Polycarbonate Sheet | same |
(1) Toggle Clamp | same |
(3) 1 1/2″ Hex Bolt (1/4-20 thread) | same |
(3) 1/4 inch Washers | same |
(6) Tee Nuts (1/4-20 thread) | (8) Sliding Tee Nuts (1/4-20 thread) |
(2) Cap Screws (50 pack) | same |
(1) Two Arm Knob McMaster Carr part #65035K41 | same |
*I use affiliate links, please see details on my disclaimer.

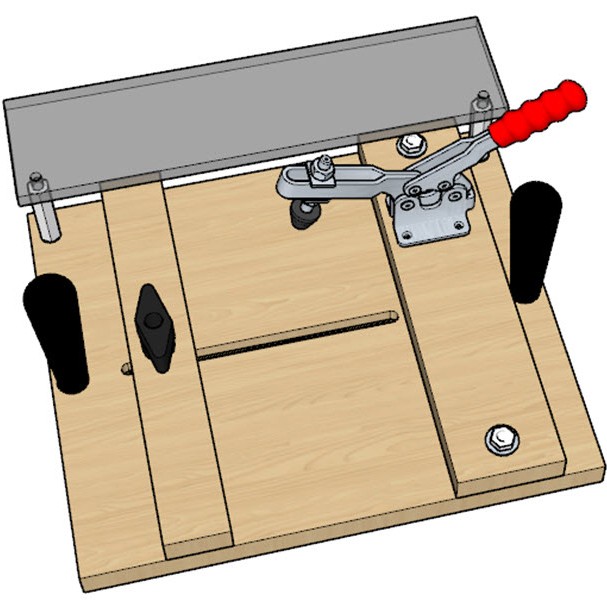
Coping Sled Plans
A coping sled is a primary jig for the router table and can help up your game when working with cope and stick door construction.
This product is a DIGITAL DOWNLOAD. You can immediately download your product off the order receipt page after the purchase. You will also immediately receive an email titled “Your MWA Woodworks order is now complete” that contains the download link in the “Downloads” section of the email.

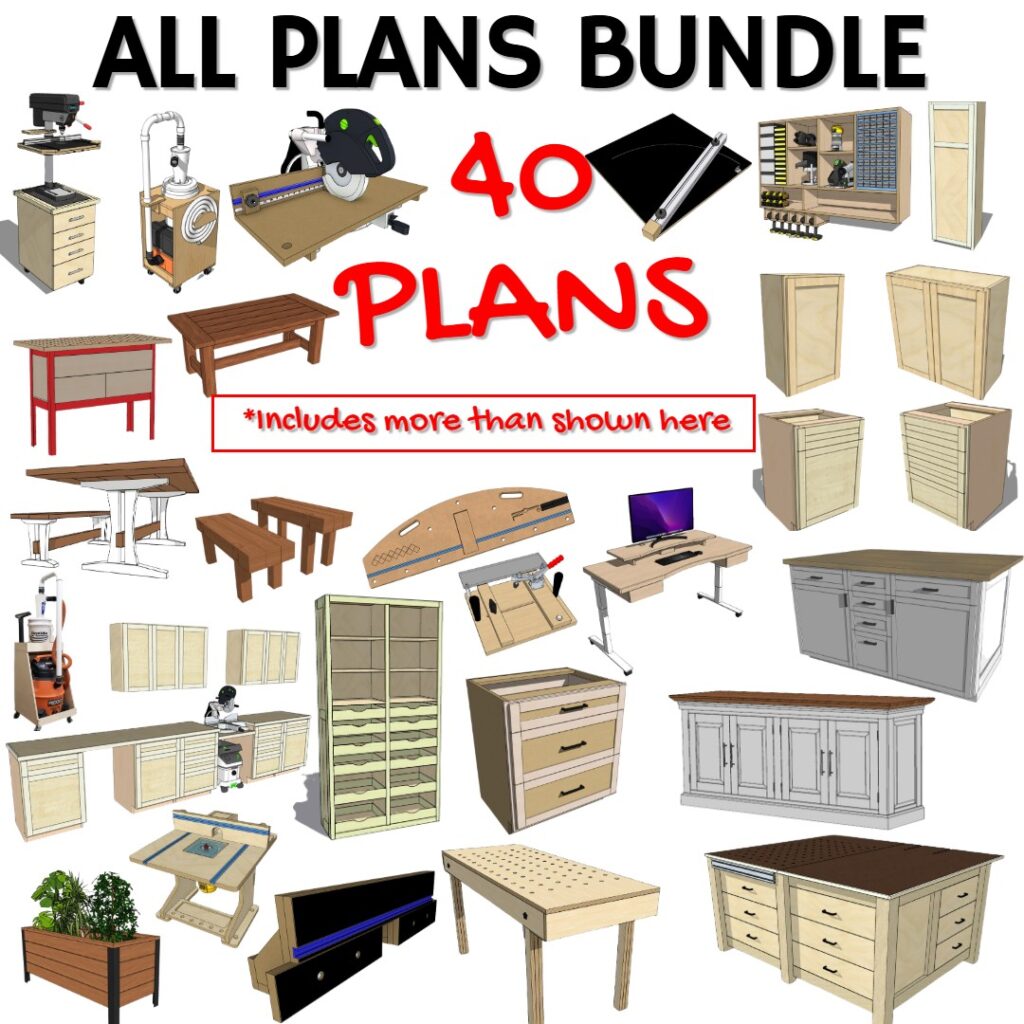
The Whole Enchilada Plan Bundle
The Whole Enchilada Plan Bundle! You want it all? You Got it! Get every plan I offer in one bundle at a savings of over 65%!
This product is a DIGITAL DOWNLOAD. You can immediately download your product off the order receipt page after the purchase. You will also immediately receive an email titled “Your MWA Woodworks order is now complete” that contains the download link in the “Downloads” section of the email.
Coping Sled Purpose
The coping sled has but one purpose but it’s an important one! Helping the woodworker make a cut across the end grain (short end) of a work piece to create a joint that allows you to build frame and panel (also called rail and stile) doors.This is a precarious cut at best and without support to back up the cut, you can easily hurt yourself or at the very least ruin your work piece.
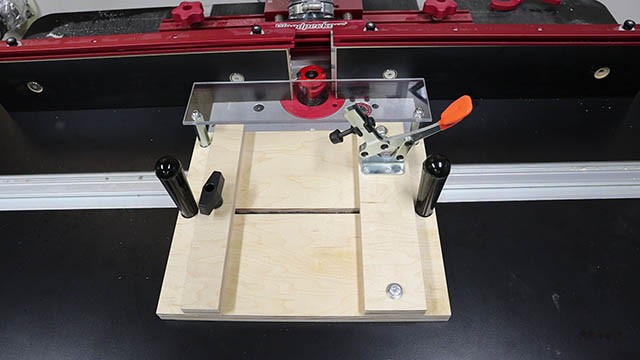
The basic anatomy of a coping sled is as follows: A base or “sled” for the work piece to ride on across the router bit, a stationary fence on the right hand side to provide sturdy support for the work piece. This fence should be squared to the sled/router table fence. Then there is a “sliding” fence on the left hand side that can lock in place to clamp the work piece horizontally and a clamp to hold the work piece down vertically. Everything is made of 3/4″ plywood. The base is 10″x 12″, the stationary fence is 3″ x 10″ and the sliding fence is 2″x10″.
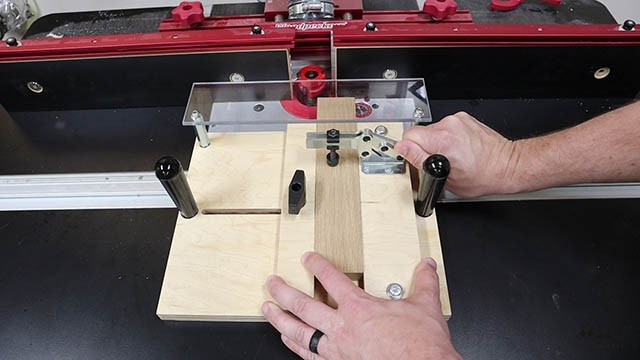
A good sled will also have two handles allowing the operator to safely move the sled and a “guide”, usually made of clear plastic that provides a straight edge to reference against the router table fence. The guide ensures that the work piece maintains the correct distance from the bit while making the coping cut.
How a Coping Sled Works

You can see here the coping sled in action. The woodworker holds the guide against the fence and from right to left smoothly guides the work piece across the router bit. A small scrap of wood can also be used to “back up” the cut between the work piece and the stationary fence. This helps eliminate blowout that can occur as the router bit exits the cut.
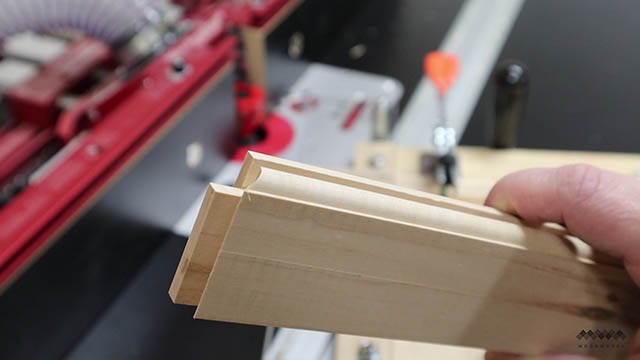
This is what my cope cut looks like. You have two parts, the “tongue” that will mate with the groove on the stile and the “cope” that will fit the contour of the inner edge of the stile.
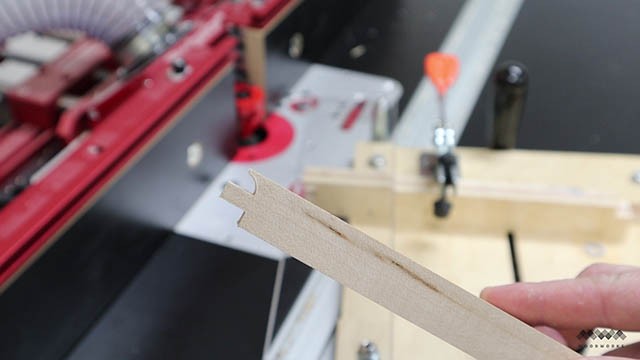
Here’s the view from the back of the work piece where you can see these two elements more clearly.
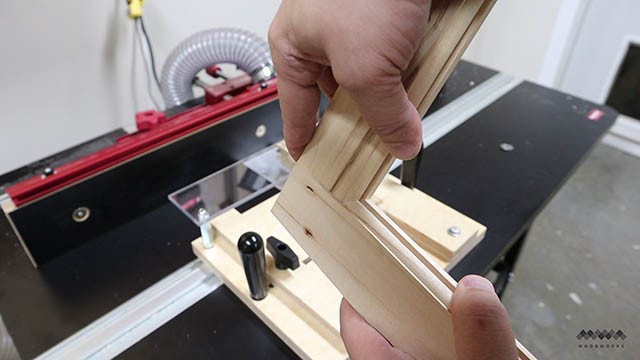
And here’s how they fit together creating a seamless joint with a perfect profiled edge!
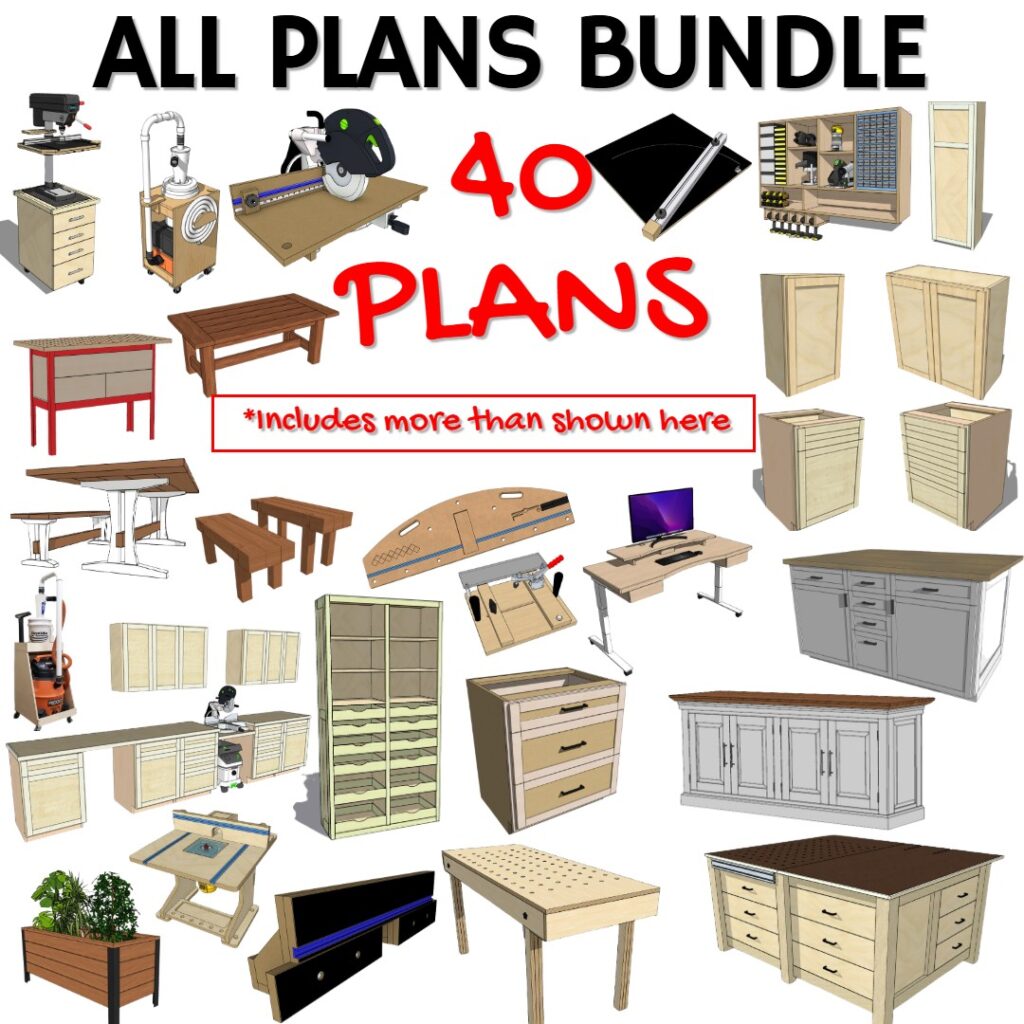
The Whole Enchilada Plan Bundle
The Whole Enchilada Plan Bundle! You want it all? You Got it! Get every plan I offer in one bundle at a savings of over 65%!
This product is a DIGITAL DOWNLOAD. You can immediately download your product off the order receipt page after the purchase. You will also immediately receive an email titled “Your MWA Woodworks order is now complete” that contains the download link in the “Downloads” section of the email.
Making a Plywood Coping Sled
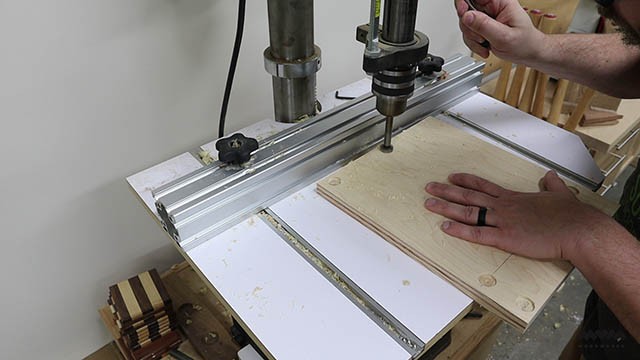
So to get started making a coping sled from scrap plywood we need to counterbore six 3/4″ holes for the tee nuts to recess into. We need two tee nuts for the guide standoffs, two for the handles and two for the stationary fence.
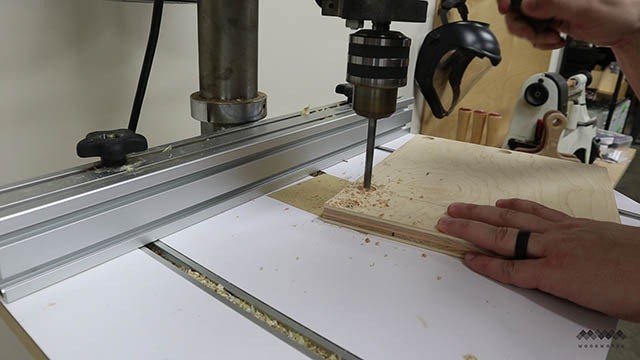
Next we drill through holes in the counterbores to allow the tee nuts to be accessed from the top side.
Creating the Groove for the Sliding Fence
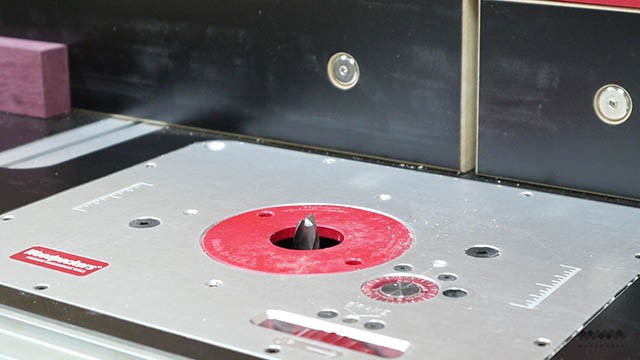
To create the groove for the sliding fence I put a 1/2″ router bit in my table and cut just deep enough for the head of a hex bolt to sit beneath the surface
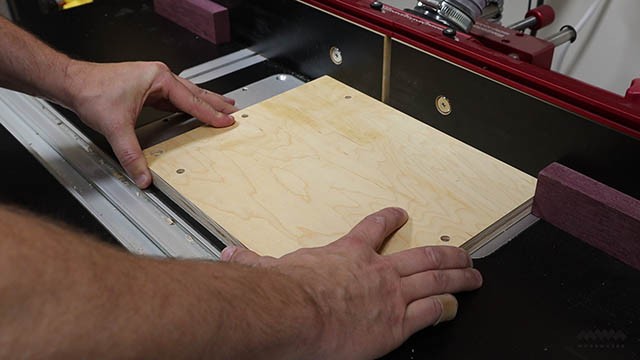
3/8 inch should be plenty of depth here but hex bolt heads may vary in thickness so check before you cut how deep the groove needs to be.
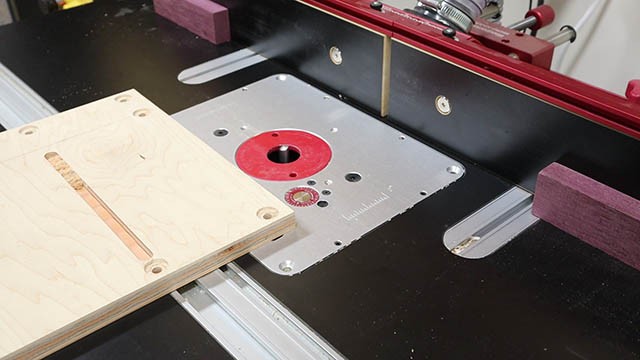
You can see here the groove taking shape
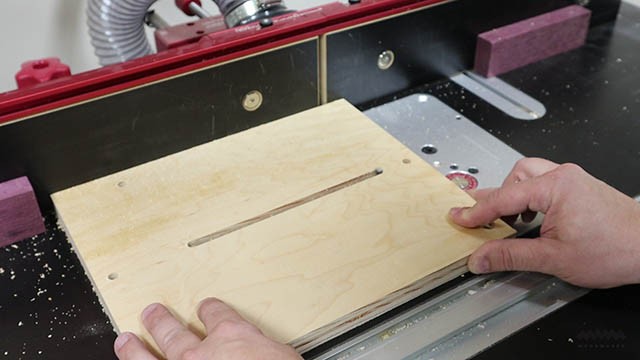
Then with a 5/16″ bit I cut all the way through the groove to allow the bolt to come through to the top, completing the sliding groove.
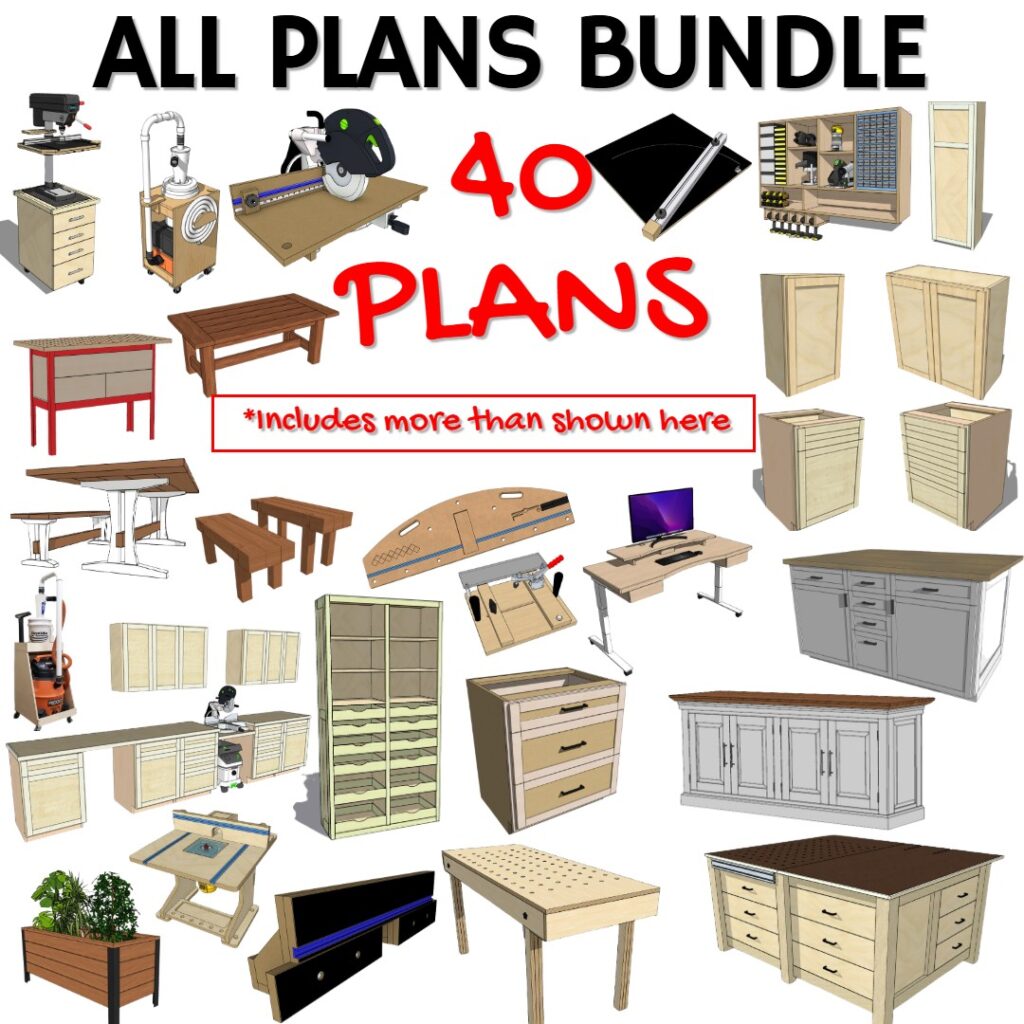
The Whole Enchilada Plan Bundle
The Whole Enchilada Plan Bundle! You want it all? You Got it! Get every plan I offer in one bundle at a savings of over 65%!
This product is a DIGITAL DOWNLOAD. You can immediately download your product off the order receipt page after the purchase. You will also immediately receive an email titled “Your MWA Woodworks order is now complete” that contains the download link in the “Downloads” section of the email.
Installing the Tee Nuts
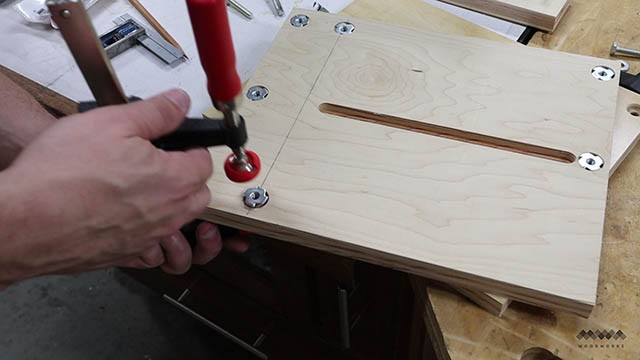
I press the tee nuts into the counterbores using a clamp. This is a fastest and easiest way I have found to do this that doesn’t involve banging them into place with a hammer/mallet.
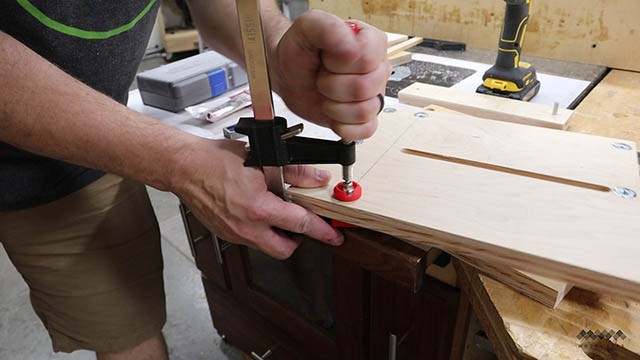
Just a few turns of the clamp easily presses them into place.
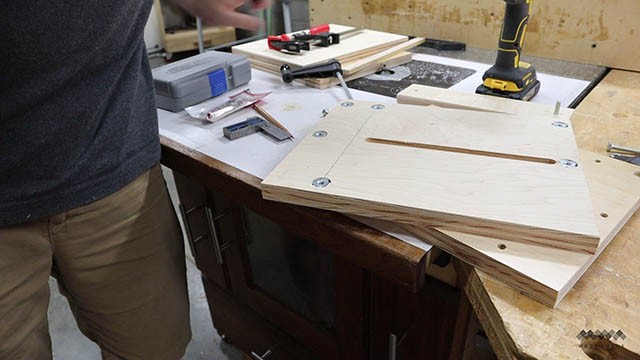
The base of the sled is now complete and we can begin assembly.
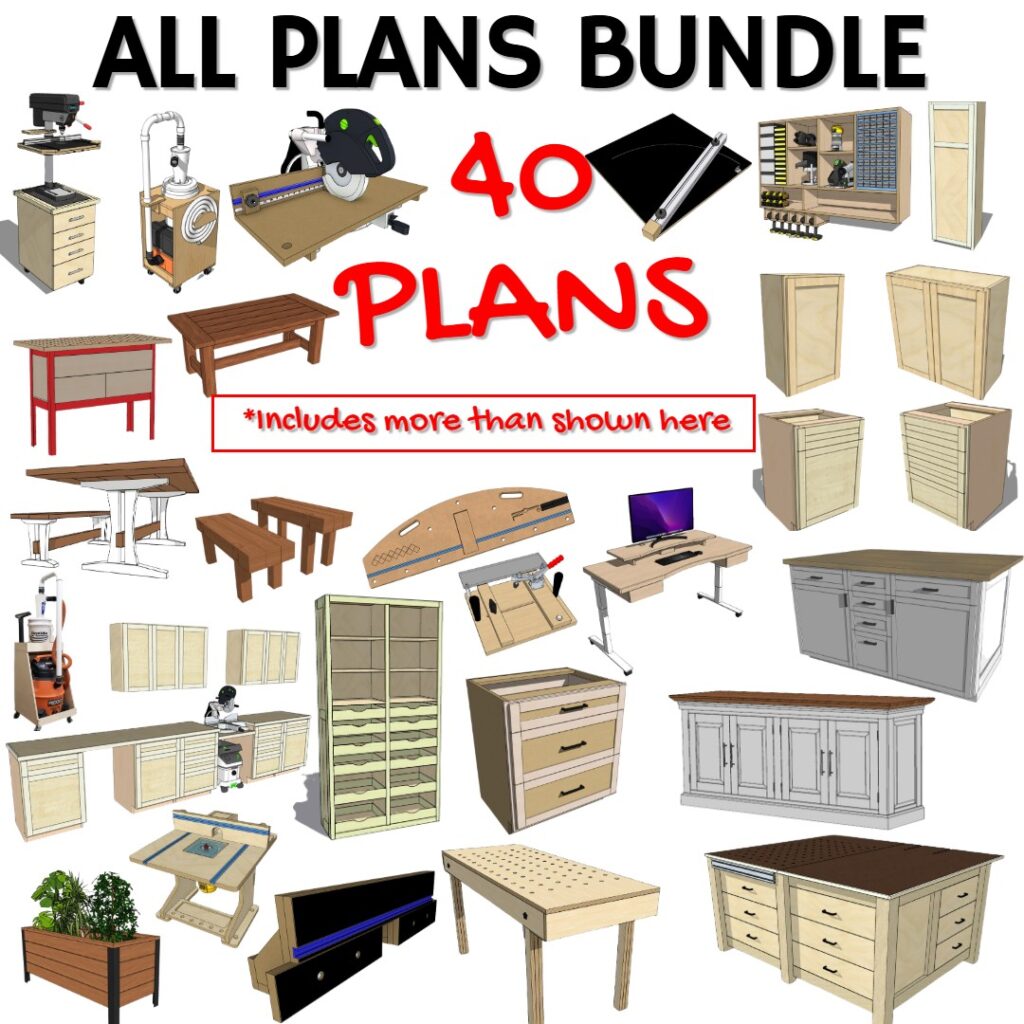
The Whole Enchilada Plan Bundle
The Whole Enchilada Plan Bundle! You want it all? You Got it! Get every plan I offer in one bundle at a savings of over 65%!
This product is a DIGITAL DOWNLOAD. You can immediately download your product off the order receipt page after the purchase. You will also immediately receive an email titled “Your MWA Woodworks order is now complete” that contains the download link in the “Downloads” section of the email.
Coping Sled Assembly
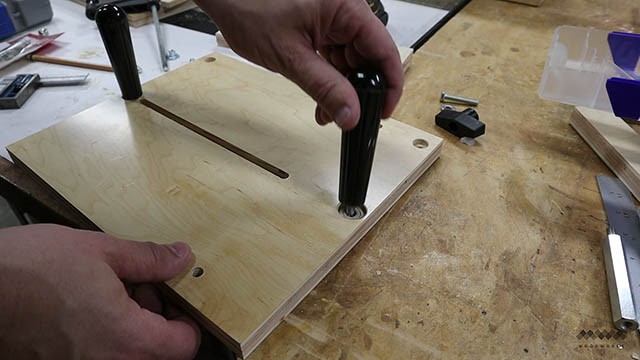
Before I move on, one note….. I did have to counterbore the spot where the handles go because the threaded stem of the handle wouldn’t reach the tee nut. You can avoid this by drilling the counterbore for the tee nuts deeper than 1/8″ like I did.
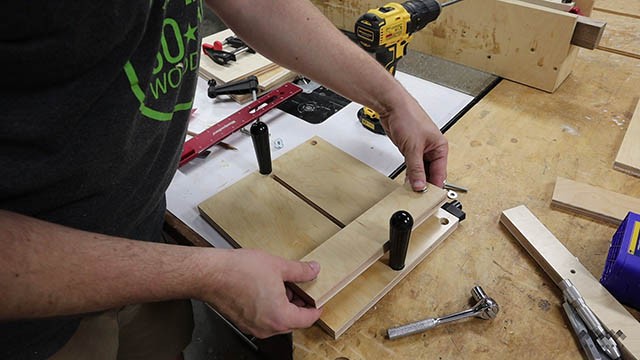
Next I install the stationary fence using two 1 1/2″ hex bolts and washers. I’m using 1/4″ 20 threaded bolts for this project.
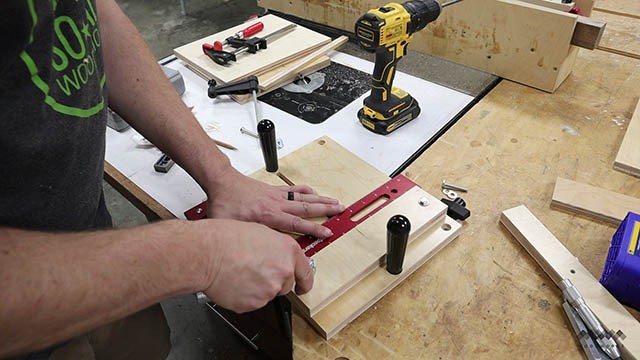
Before you fully tighten the fence down ensure that the fence is squared to the sled. This is achievable my making the holes in the fence 5/16″ in diameter, creating a little wiggle room for the 1/4″ bolts to move in.
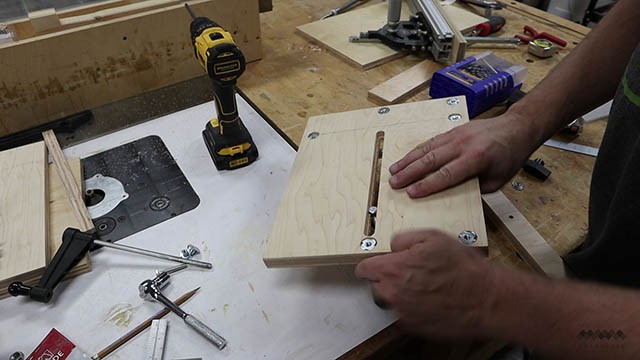
Next add another 1 1/2″ bolt to the groove on the underside of the sled. Add a washer here if you want (I didn’t) but it can make things slide better sometimes.
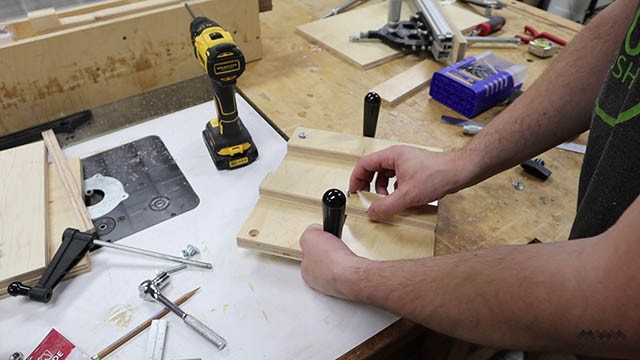
Now drill a 1/4″ hole in the center of the sliding fence and slip it over the bolt. Add a washer to this side.
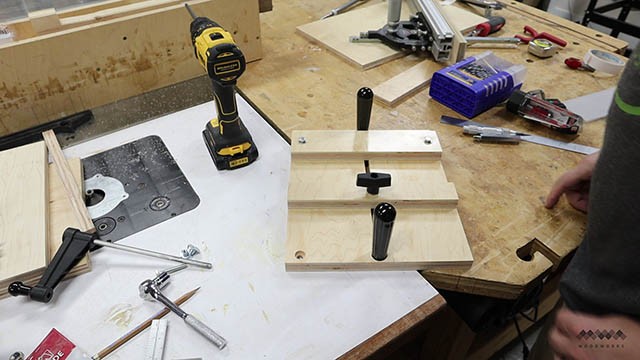
Then add a knob to the top to tighten the fence in place when needed.
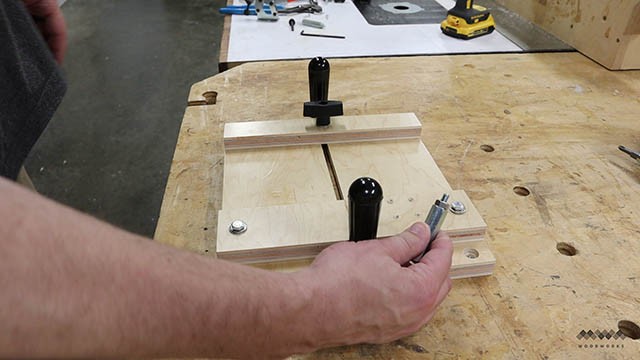
Next add the 2″ hex standoffs. These little guys have a threaded “male” side and a threaded “female side”. Male side goes down to connect to the tee nut. I had to add 1/4″ hex nuts to act as spacers because the male threads were too long and bottomed out before the standoff was tightened down fully.
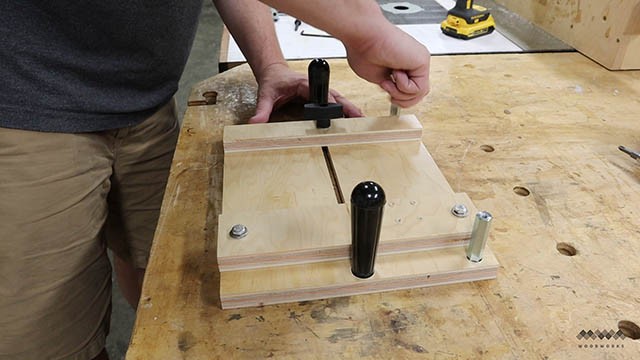
The “female” end should be facing up for the next step.
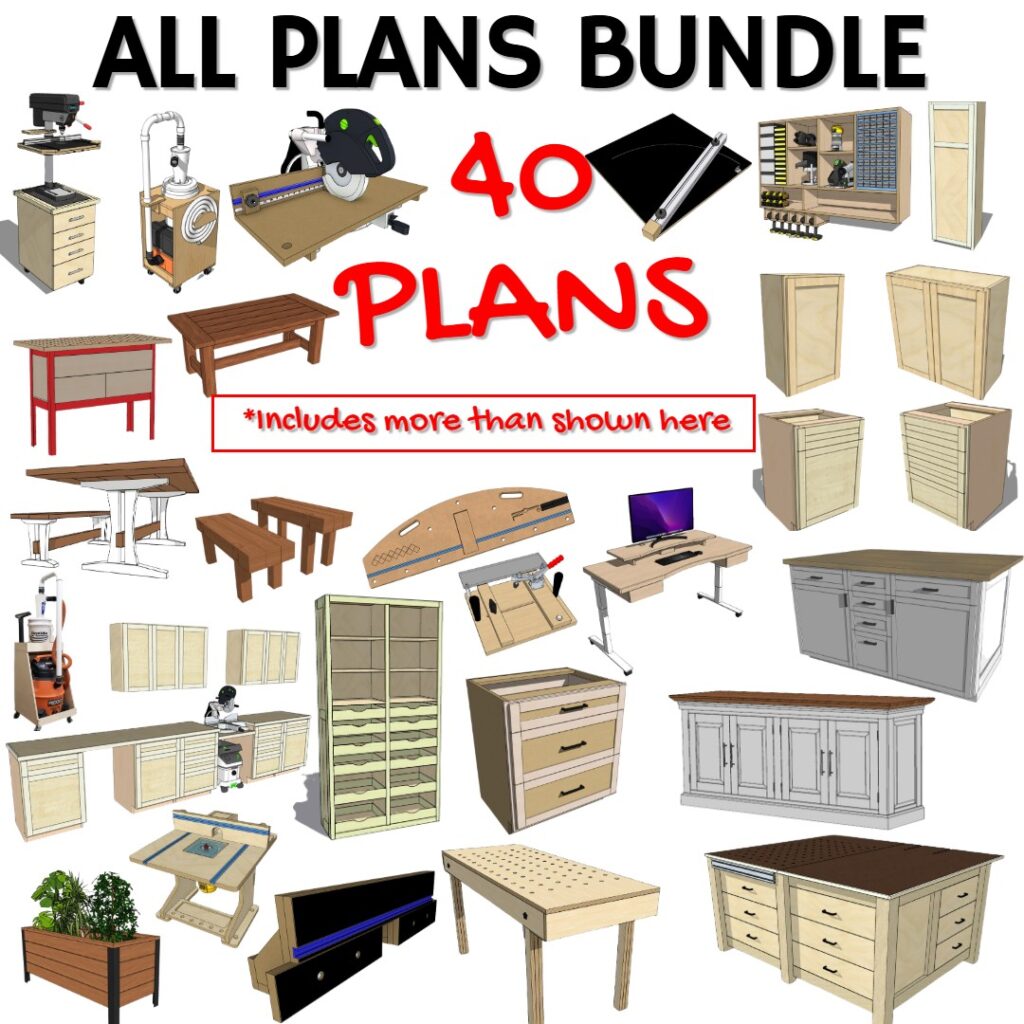
The Whole Enchilada Plan Bundle
The Whole Enchilada Plan Bundle! You want it all? You Got it! Get every plan I offer in one bundle at a savings of over 65%!
This product is a DIGITAL DOWNLOAD. You can immediately download your product off the order receipt page after the purchase. You will also immediately receive an email titled “Your MWA Woodworks order is now complete” that contains the download link in the “Downloads” section of the email.
Making a Guide for the Sled
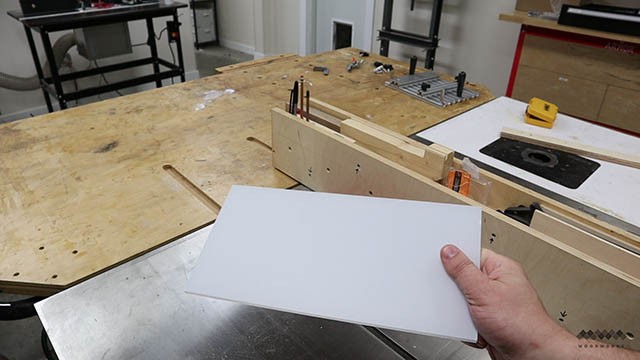
Next I need to add the guide and I’m using a 6″x12″ piece of 1/4″ polycarbonate (clear plastic) for my guide.
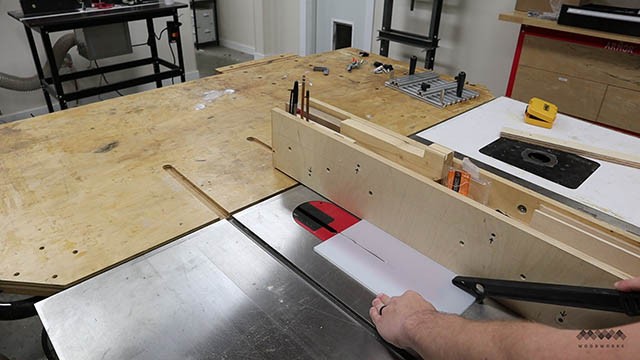
First I need to cut it in half lengthwise to make a 3″x 12″ piece. This is easily done at the table saw.
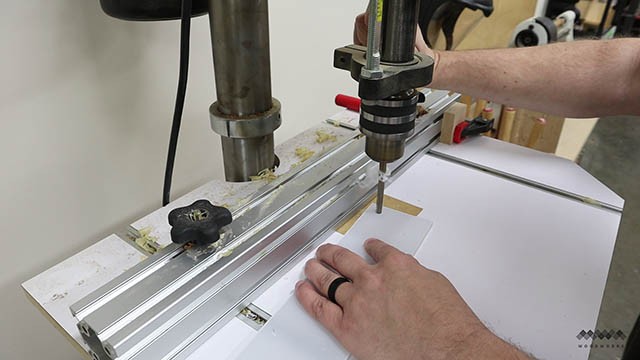
I then add two 1/4″ holes to each end. These holes are offset 1/2″ from the side and 3/4″ from the back edge of the polycarbonate sheet.
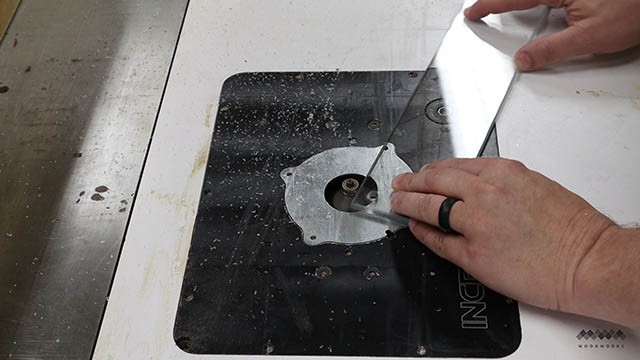
I then peel off the protective film and chamfer the (very) sharp edges of the polycarbonate. This will prevent annoying cuts to the knuckles down the road.
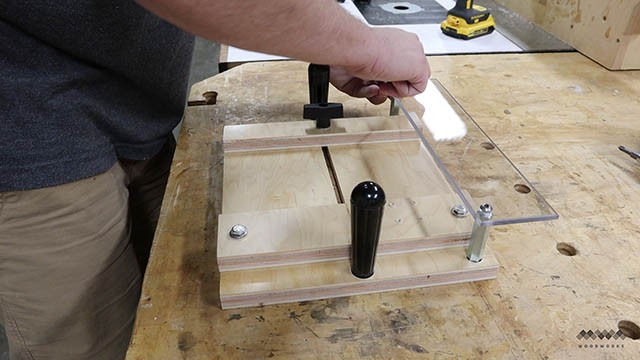
I then installed the guide on top of the standoffs using hex drive cap screws. These screws were 1/2″ long and also 1/4″ 20 threads to mate with the female end of the standoffs.
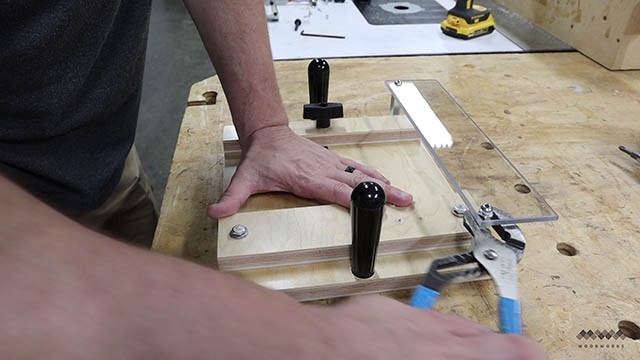
To successfully tighten everything down without cracking the polycarbonate, you should leave the cap screws loose and tighten the standoffs all the way, then go back with a hex wrench and tighten the cap screws snugly in place.

The sled is nearly complete! Just one more thing…..
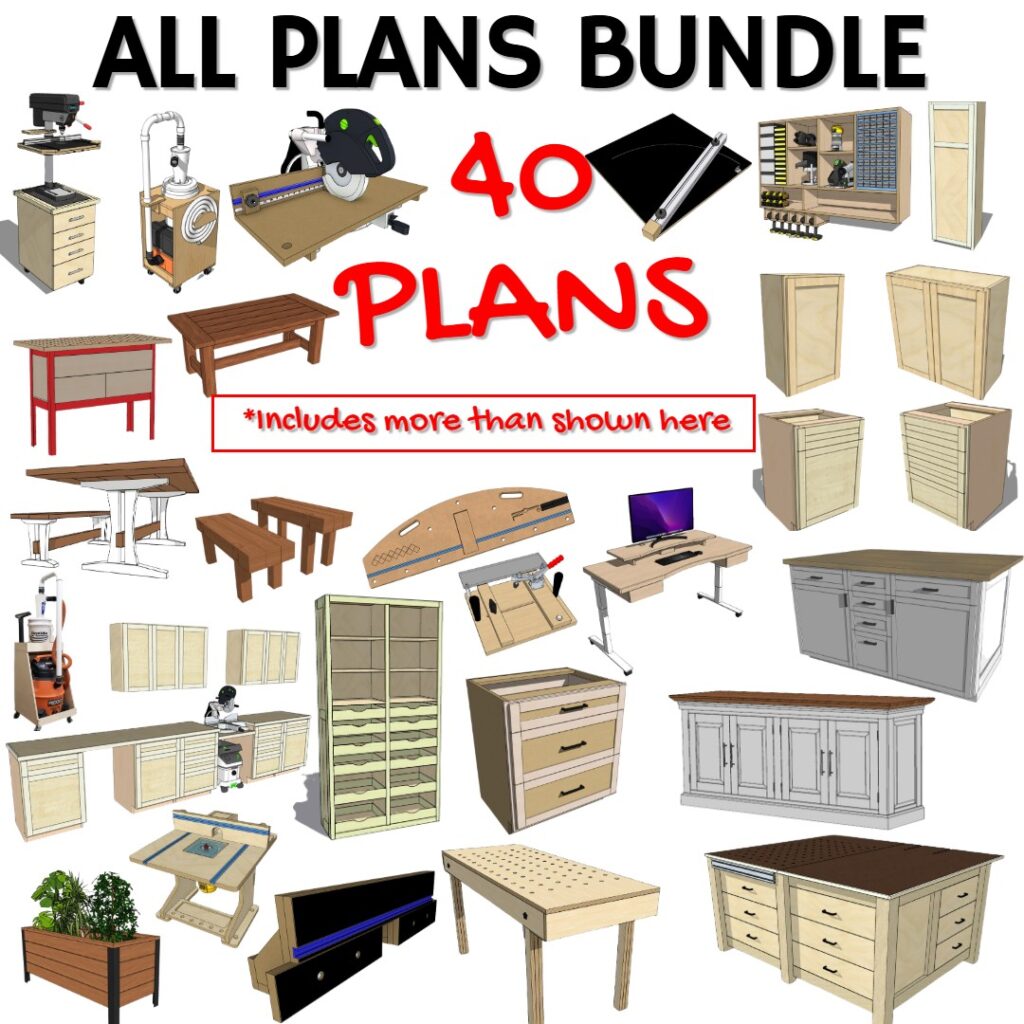
The Whole Enchilada Plan Bundle
The Whole Enchilada Plan Bundle! You want it all? You Got it! Get every plan I offer in one bundle at a savings of over 65%!
This product is a DIGITAL DOWNLOAD. You can immediately download your product off the order receipt page after the purchase. You will also immediately receive an email titled “Your MWA Woodworks order is now complete” that contains the download link in the “Downloads” section of the email.
Adding the Toggle Clamp
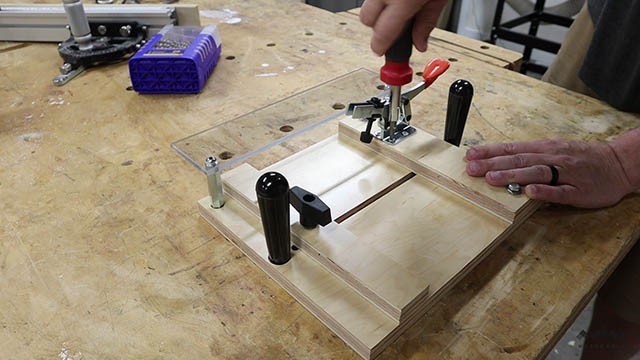
I need to add the toggle clamp to the stationary fence. This will allow me to clamp down on the work piece to keep it from moving as I make the cope cut.
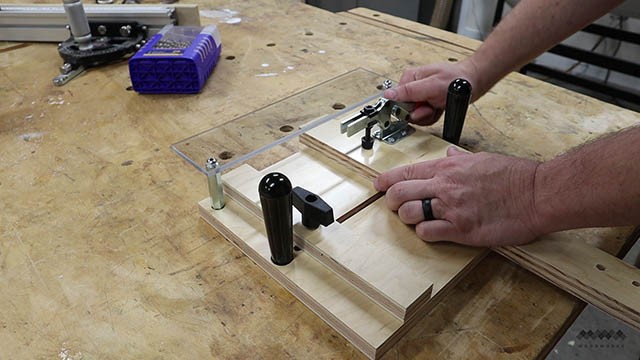
You can see here how it will secure the work piece and can be adjusted for thicker material if needed, just adjust the clamping bolt.
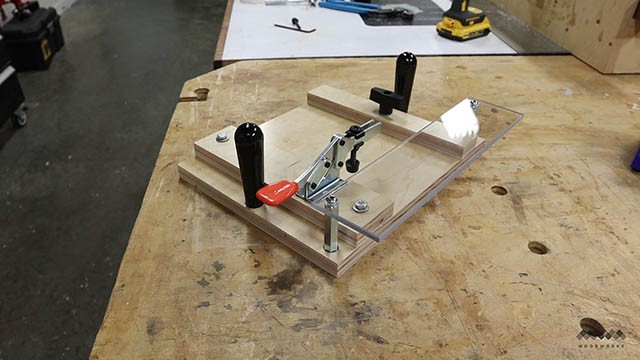
That’s it! The plywood sled is complete. It can accommodate work pieces up to 5 1/2″ wide. If you need more, just make the base wider! Easy peasy.
No Plywood Scraps? Use Aluminum Extrusions!
What if you don’t have the plywood scraps to make this jig? You probably wont want to buy an entire sheet just to make one small jig. Never fear, there’s a better (and cheaper) way! You can use aluminum extrusions to form the base and the two fences. Note that I purchased these from a company called Misumi (links above) and the great part is they have tracks built right into them for fastening all the hardware!
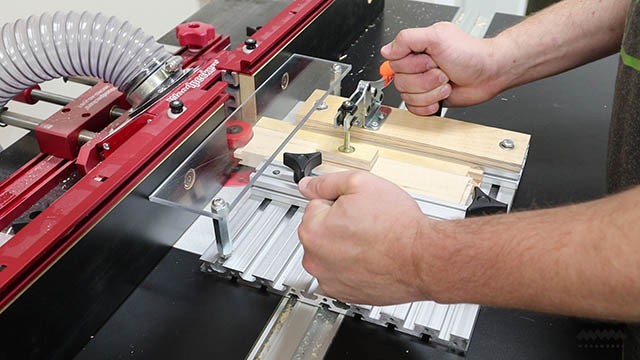
For simplicity, I used all the same hardware as I did for the plywood sled (handles, standoffs, toggle clamp and polycarbonate). The only difference was that I swapped out the tee nuts for sliding tee nuts (more below on that).
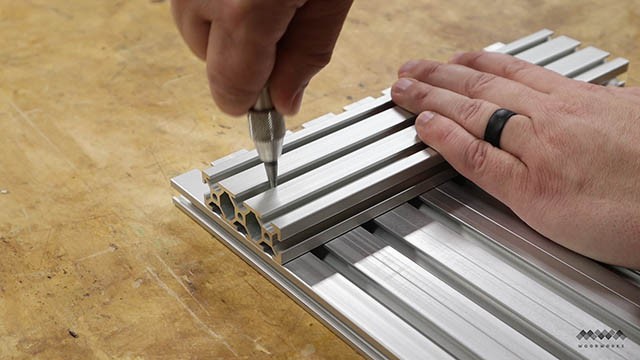
There’s really not much work to be done before assembly. You really just need to drill the holes in the fences to allow bolts to reach the base.
Marking out and Drilling Holes
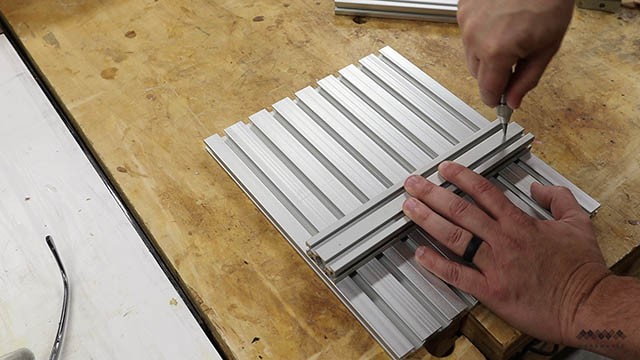
You want to mark the hole locations right over the two outside tracks in the base. you can mark the soft aluminum using a center punch. Do this for both the stationary rail and the sliding rail.
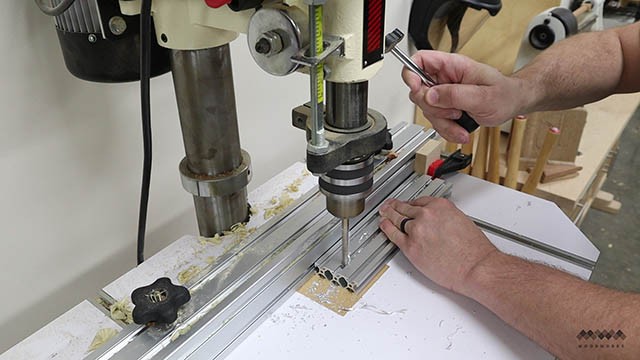
Did you know that you can cut aluminum with regular woodworking blades and drill bits? Its true and that makes this an easy job! You can use a handheld drill for this but a drill press will help you be more accurate.
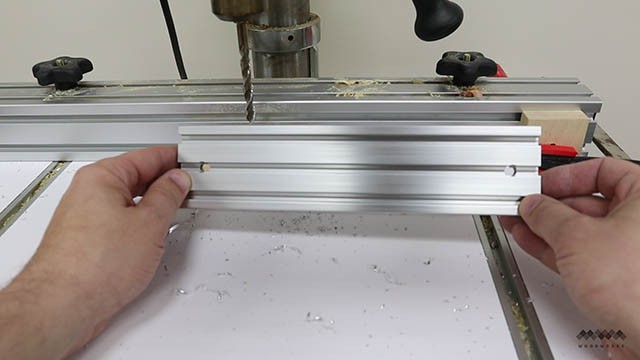
Just add the 5/16″ holes to the stationary fence and the sliding fence.
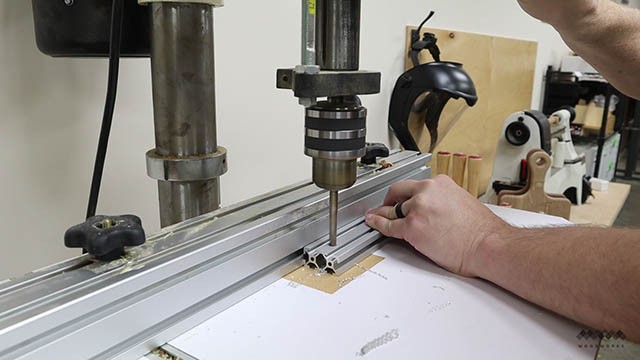
NOTE: the sliding fence really only needs one hole in the center. I originally made this sled first thinking two holes/knobs was best but it ends up being more difficult to move the fence.
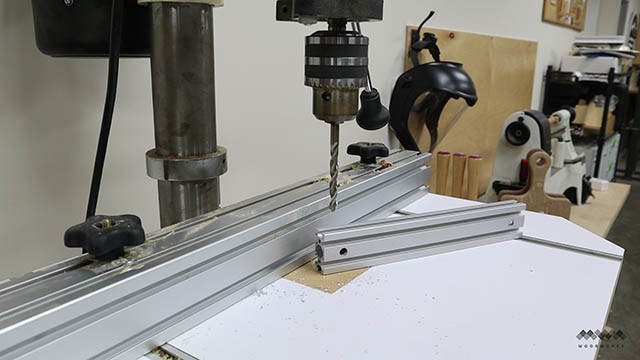
Here you can see how cleanly aluminum cuts just with regular twist drill bits!
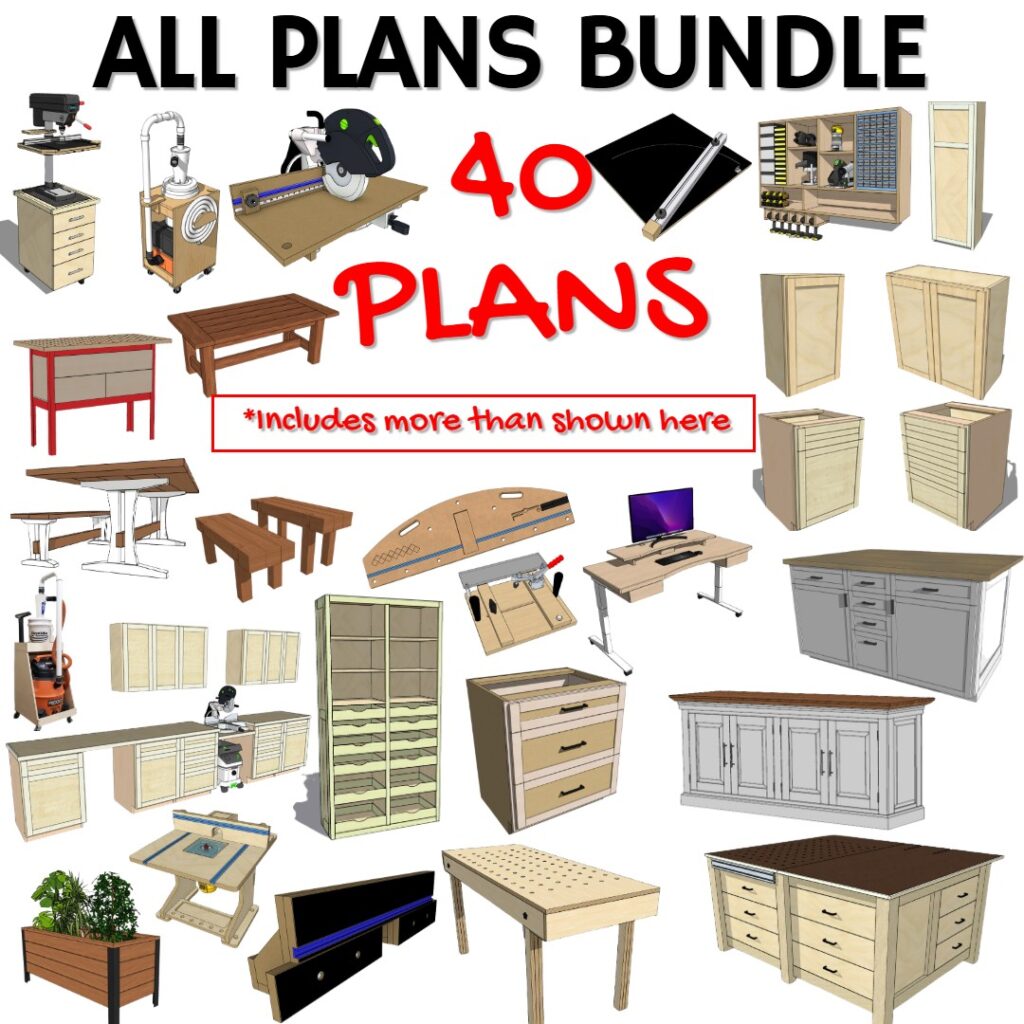
The Whole Enchilada Plan Bundle
The Whole Enchilada Plan Bundle! You want it all? You Got it! Get every plan I offer in one bundle at a savings of over 65%!
This product is a DIGITAL DOWNLOAD. You can immediately download your product off the order receipt page after the purchase. You will also immediately receive an email titled “Your MWA Woodworks order is now complete” that contains the download link in the “Downloads” section of the email.
Assembling the Coping Sled
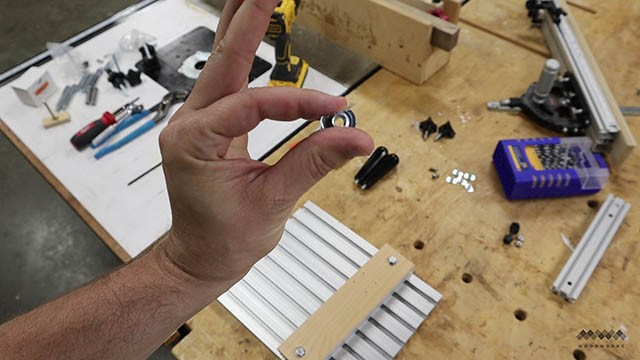
OK, everything will be attached using sliding tee nuts. These are different that regular tee nuts because these have a smooth rectangular bottom that can slide in the grooves of the aluminum base! So useful!
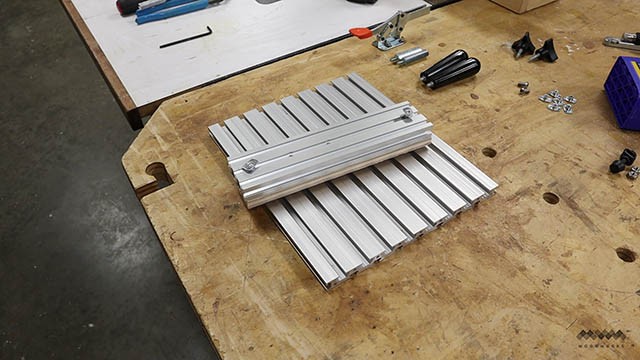
OK, good news is that all we have to do now is assemble this thing! First I add the stationary fence. Using the 1 1/2″ hex bolts With a washer on top and a sliding tee nut on the bottom.
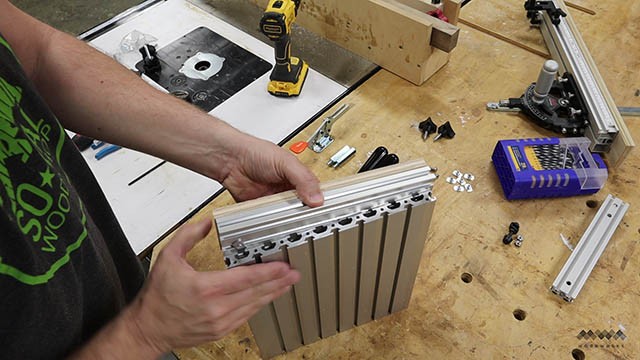
I slide the fence into the tracks in the base.
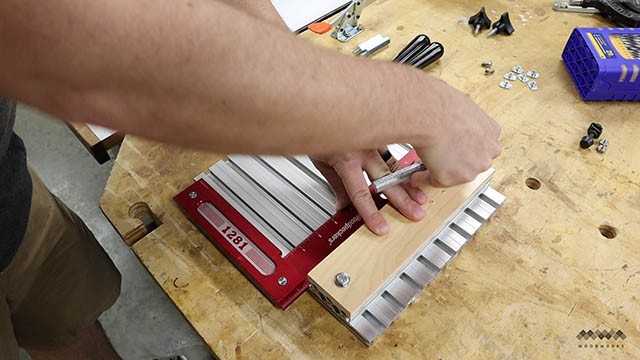
Like before, I square the fence and tighten it down snugly.
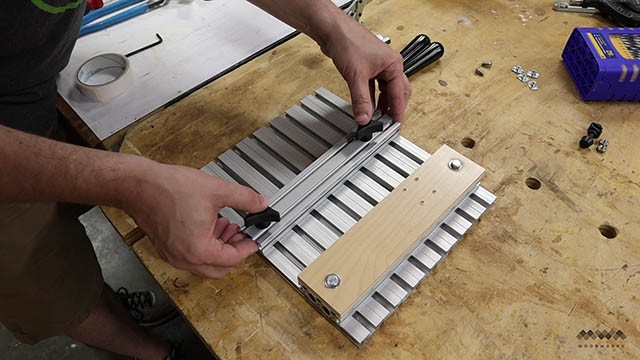
I then repeat adding the sliding fence.
A Small Unnecessary Modification
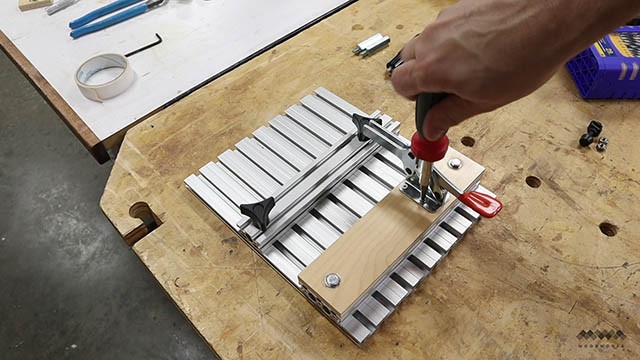
I then add the clamp to the stationary rail. Your eagle eye might notice that bit of plywood on top of the fence. You may be asking yourself “I thought I didn’t need scraps for this version of the sled”? Well you’re right, you don’t. But I couldn’t decide where I wanted my clamp to go and before I made a bunch of holes in my nice aluminum fence I decided to add some plywood to the top to make it easier to move the clamp if I felt I needed to. You can fasten the clamp directly to the aluminum fence using regular steel screws just as you would to plywood. Also note that adding the plywood (and extra height) will cause another challenge for us to solve in a minute or two…….
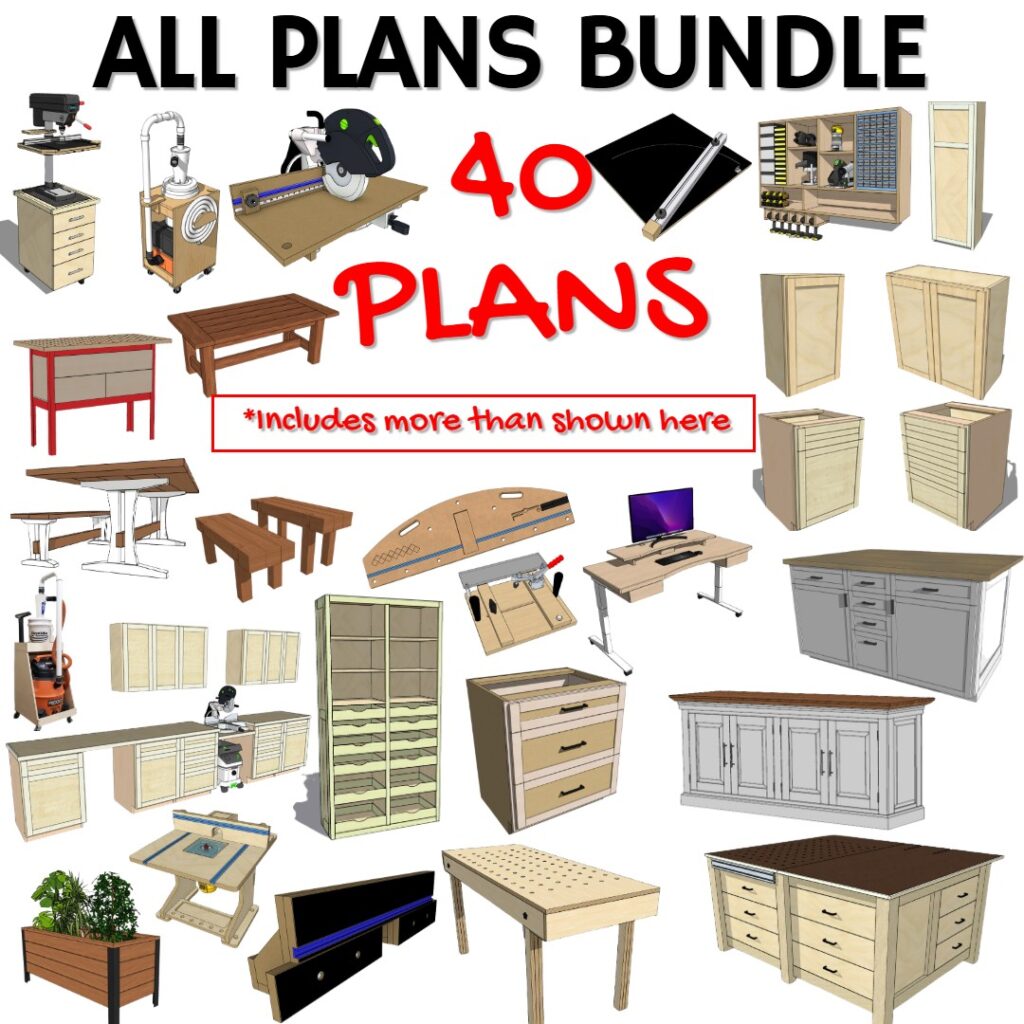
The Whole Enchilada Plan Bundle
The Whole Enchilada Plan Bundle! You want it all? You Got it! Get every plan I offer in one bundle at a savings of over 65%!
This product is a DIGITAL DOWNLOAD. You can immediately download your product off the order receipt page after the purchase. You will also immediately receive an email titled “Your MWA Woodworks order is now complete” that contains the download link in the “Downloads” section of the email.
Continuing On…..
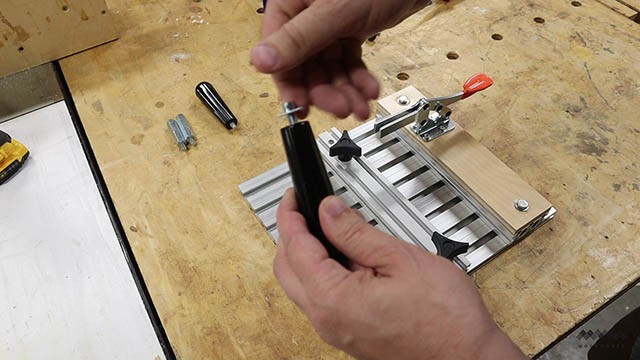
Now I just add sliding tee nuts to the handles….
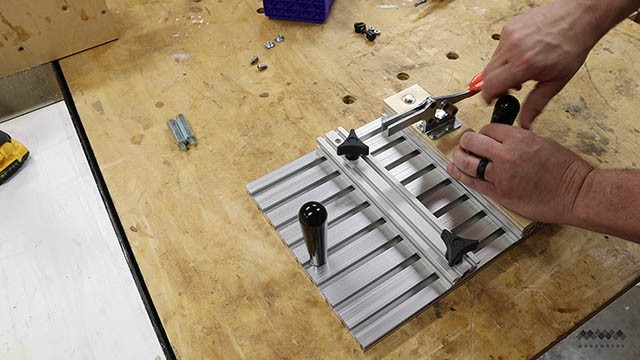
….and slide them into place. This is one nice thing about the aluminum version. You can move these handles from one track to another based on where you want the handles located (closer or further from the bit).
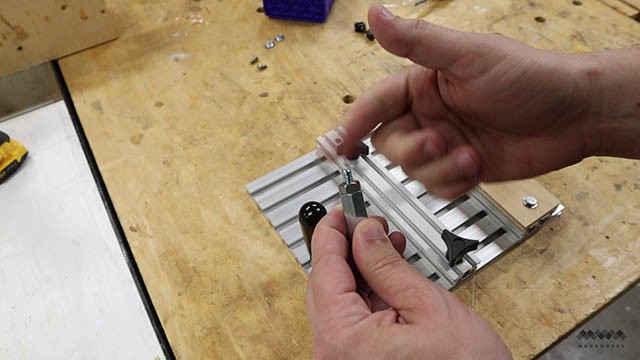
Now install the standoffs (again using a hex nut as a spacer).
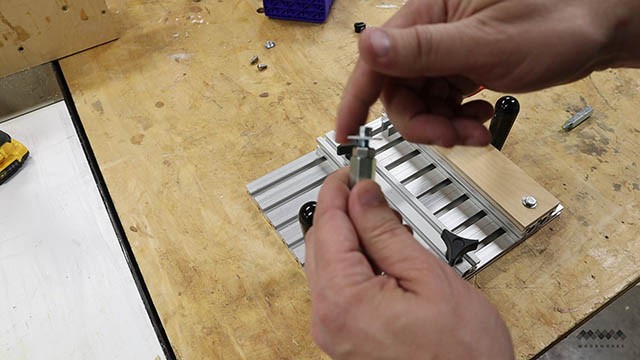
Add your sliding tee nut next
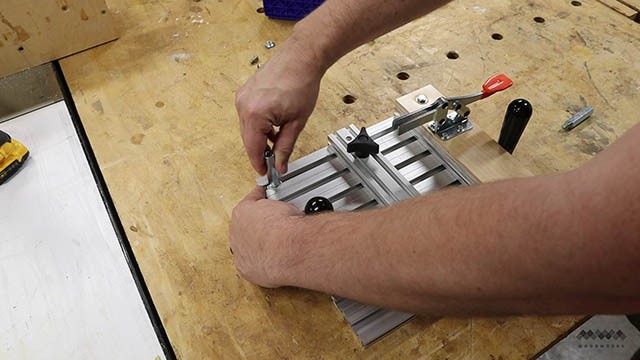
Then slide them onto the front side of the sled.
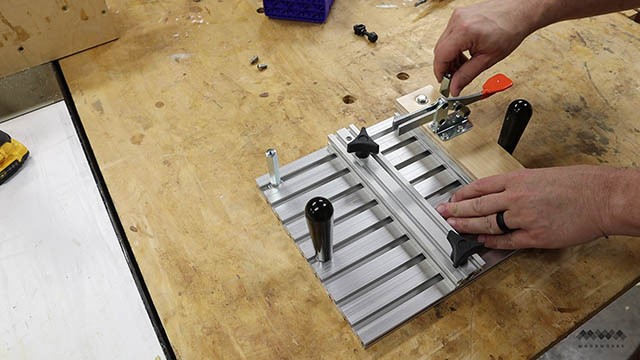
These again can be moved if you want to adjust the position of the guide forward or backward.
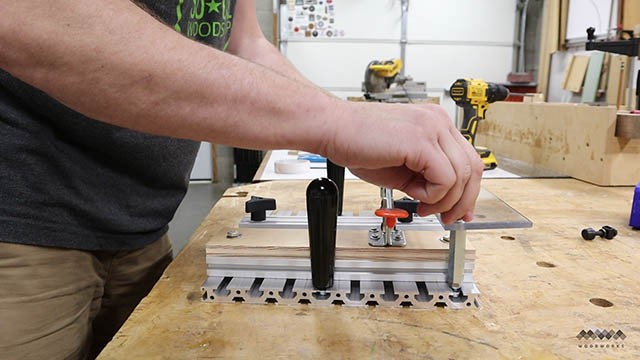
Next install the polycarbonate guide the same as in the previous sled. First tighten the standoffs and then go back and tighten the cap screws.
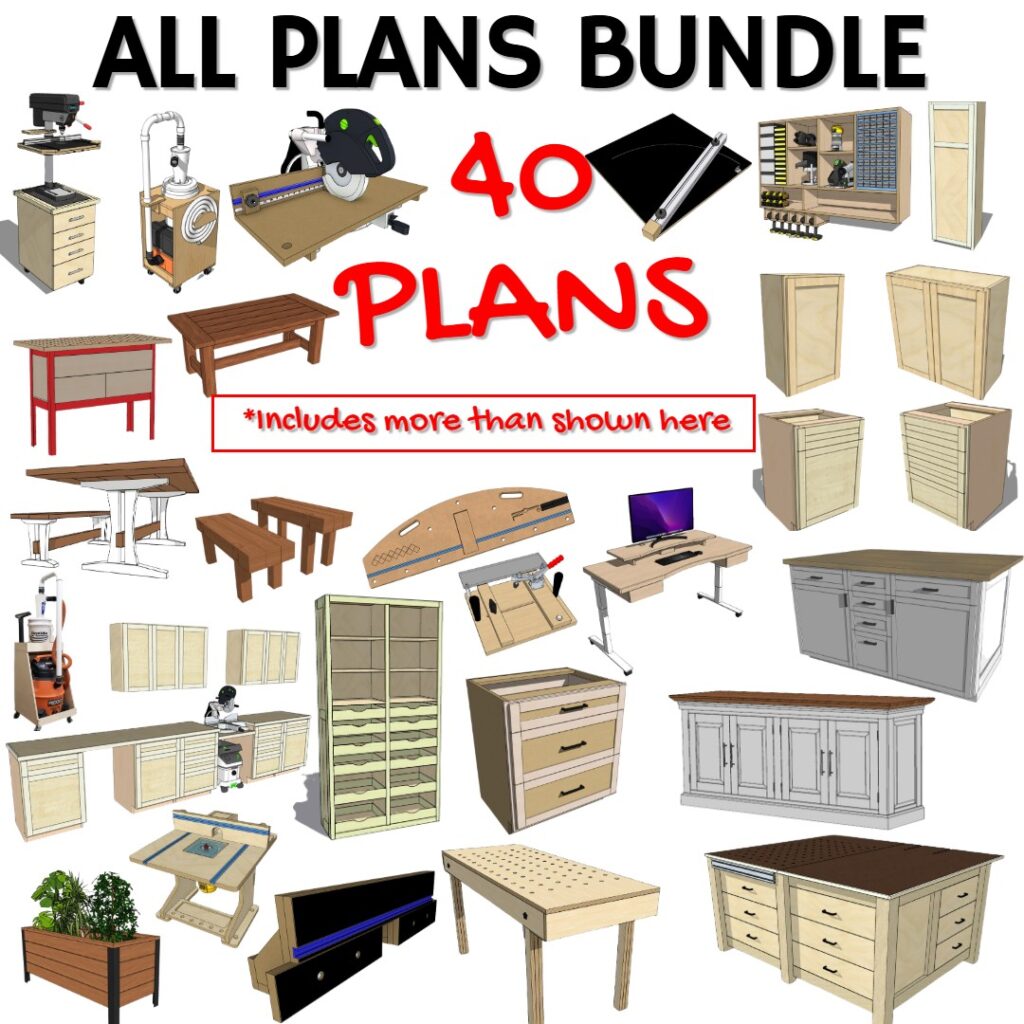
The Whole Enchilada Plan Bundle
The Whole Enchilada Plan Bundle! You want it all? You Got it! Get every plan I offer in one bundle at a savings of over 65%!
This product is a DIGITAL DOWNLOAD. You can immediately download your product off the order receipt page after the purchase. You will also immediately receive an email titled “Your MWA Woodworks order is now complete” that contains the download link in the “Downloads” section of the email.
Solving the Clamp Height Problem I Created
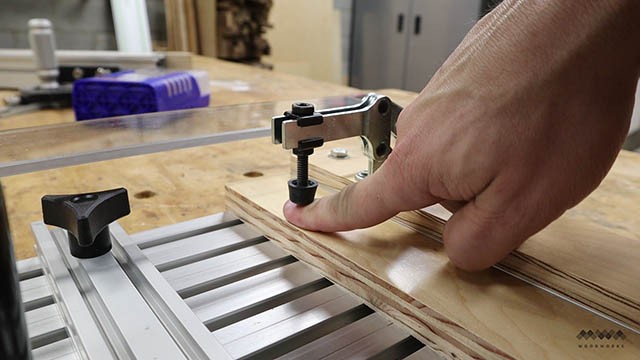
Here, though, is a problem. Because I added the extra plywood to the stationary fence, the clamping bolt wont reach the work piece. But I solved this by using a longer tee bolt. If you don’t know what a tee bolt is, it’s a bolt that has what looks like a sliding tee nut for a head. It serves the same purpose allowing you to make jigs that have sliding components.
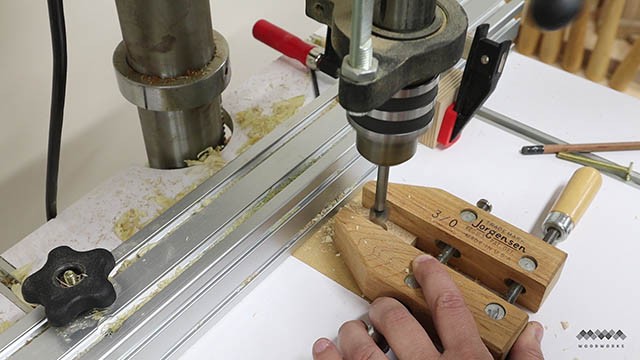
Next, I made my own clamping bolt by taking a small scrap of ply and making a recess that the bolt head could fit into about 3/8″ deep.
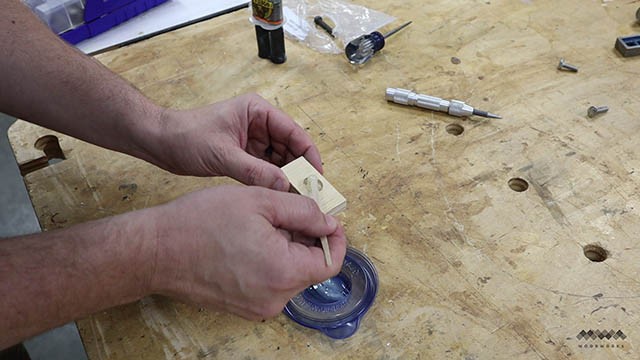
Then , I mixed up a small amount of epoxy and put it into the recess.
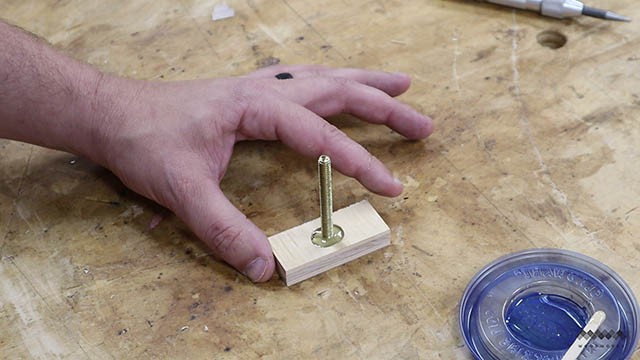
Finally, I then sunk the head of the tee bolt into the epoxy and let it cure.
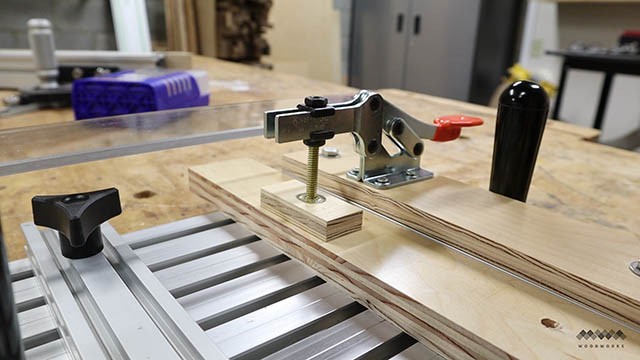
Now I have a clamping bolt that can reach my work piece! Problem solved!
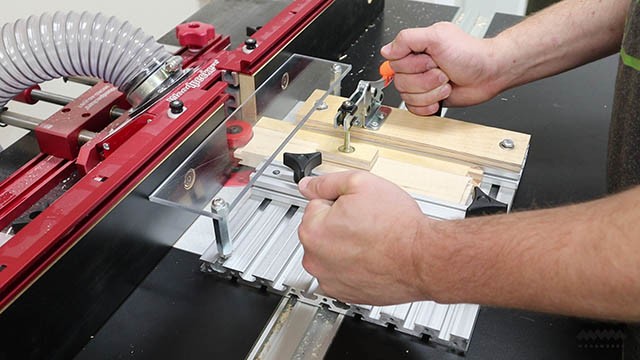
This sled is much more stout and has the ability to configure the handle and standoff positions making it a nicer version of the coping sled. The aluminum extrusions do add to the cost but they are a cheaper way to go than buying a new sheet of 3/4″ plywood if you don’t have the scraps on hand.
I built your design of this sled, and I really like it I decided to pay for the plans to support your efforts. I did add a second toggle clamp to hold the sacrificial piece behind the stock piece.
For years I just used another piece of wood to hold the stock that I was cutting up against. It worked, was it the safest way to cut the end grain On the rail? No but it was effective for me. And I had no mishaps. Now I can route the rails safely now. And it beats paying $$$ for a Commercial variant.
Lane,
Hey that’s great to hear! That’s why I try to help others!
Great tool to have in your shop, the only thing is that I used a piece of Phenolic for the base instead of plywood or aluminum. It slides so much smoother than plywood and it’s probably just a little less expensive than the aluminum extrusion.
You can get it at Woodcraft the size of the sheets are larger than what you need, I used the extra for other jigs in the shop.